Ultrasonic welding
What are ultrasonics?
From the tweeting of birds to glass-shattering screams – sound is more than just what we can hear with our ears. It's created by the mechanical vibration of bodies. This doesn't just happen in the air, but in every elastic medium, i.e. gases, liquids, and solids.
Ultrasonics are an example of the fact that humans cannot hear every type of sound. High-frequency sound waves are used in industry and medicine, and these cannot be heard.
Sound waves are categorized by their frequency (number of waves per second). For example, ultrasonics range from 20 kHz to 1 GHz. Ultrasonic welding uses frequencies from 20 kHz to 70 kHz. The lowest range of this can still just be heard by human ears. This is because audible sound (for humans at least) has a range of only from 16 Hz to 20 kHz. At most, oscillations going above this are perceived as vibrations.
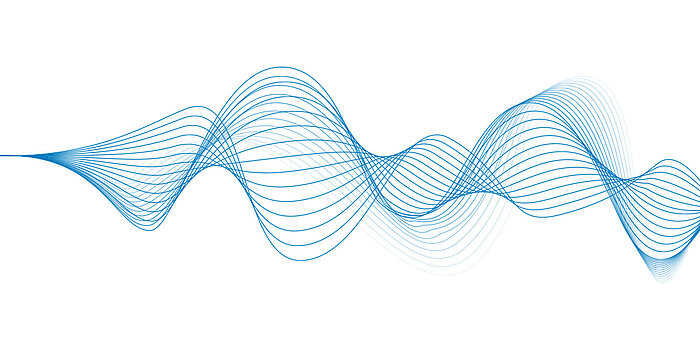
How does ultrasonic welding work?
When the ultrasonic vibrations hit a material (e.g. a plastic), the molecular chains start to oscillate. The molecules start to move and rub against each other. This generates energy (referred to as friction heat). In the case of thermoplastic materials, this process causes them to start to melt. Ultrasonic welding takes advantage of this principle. After a short hold time under additional pressure, various materials (components) can be welded together at a molecular level in the joining area.
What is ultrasonic welding suitable for?
Ultrasonic welding happens in split seconds without the need for any aids such as adhesives or screws. Ultrasonics are used to create packaging, car parts, toys and much more, for example, by:
- Joining injection-molded parts (e.g. for toys)
- Embedding membranes (e.g. for filter membranes in medical components)
- Fusing leather, nonwovens and textiles (e.g. air filters in cars)
- Staking different types of materials together (e.g. for airbags)
- Creating form-fit joints using a shaping technique (e.g. for magnet contacts in chargers)
- Countersinking sockets and magnets (e.g. encapsulated magnets for activating sensors)
The ultrasonic welding system
The complete ultrasonic welding system consists of various components. The active components generate the vibrations, transfer them, and apply them into the weld joints. The passive components absorb the resulting forces, hold the parts in position, and particularly support the weld joint point at which the components are joined together.
Active:
Amplitude transformer (booster or amplitude coupler)
The converter, booster, and sonotrode are combined to form what is referred to as the stack.
Passive:
Process technology: The principle of energy focusing
In order to melt the component with precision, the vibration energy must be made to converge on one point. This is called energy focusing. This specific point is where the heat development is strongest and melting occurs – for a defined weld process with low energy consumption.
Types of energy focusing
Everything is a question of shape: To make the vibration energy converge at the correct point, the geometry of the parts to be welded or the tools must be designed accordingly. For component-integrated focusing, energy directors (ED for short) focus the energy at the materials themselves. For focusing tool geometry, the tools are shaped for the specific application.
In joint design, the energy is focused by the shape of the components. Here, the area at which both parts are to be joined is given a specific shape. In most cases, there is a tip or an edge at this point. This is precisely where the energy is focused, which is why these parts are called energy directors (ED for short).
The most important process parameters for ultrasonic welding
Tight, sturdy and visually appealing – to create the perfect weld joint, the weld tool, material, and weld process must be coordinated with each other. The settings are key: The right process parameters ensure optimal and reproducible results.
The trigger point defines the start of the weld: The sonotrode presses down on the component with the trigger force. If this only yields to a minimal extent over a specific period of time, the ultrasonics are triggered and the trigger force switches to weld force. This ensures that the start point of the welding always remains the same, and the quality of the results remains consistently high.
Which materials can be welded using ultrasonics?
Generally speaking, most thermoplastic materials (plastics which can be shaped when heat is applied) can be welded with ultrasonics. The harder the material, the better. As well as plastics, different nonferrous metals such as aluminum, nickel, brass, and copper are also suitable for ultrasonic welding.