Weldable metals
Ultrasonic welding is suitable for joining similar materials but can also be used for joining dissimilar materials. There are different welding techniques, for example, laser, gas, or ultrasonic welding. When metals are welded using ultrasonics, these are joined by the introduction of ultrasonic waves. This is a quick and especially energy-efficient process.
Ultrasonic welding technology for nonferrous metals
In ultrasonic welding, it is mainly nonferrous metals such as aluminum, silver, copper and nickel which are used. Nonferrous metals are all pure metals apart from iron as well as alloys (compounds of various metals), which have an iron proportion of 50% of less. Pure ferrous metals are not used in ultrasonic welding.
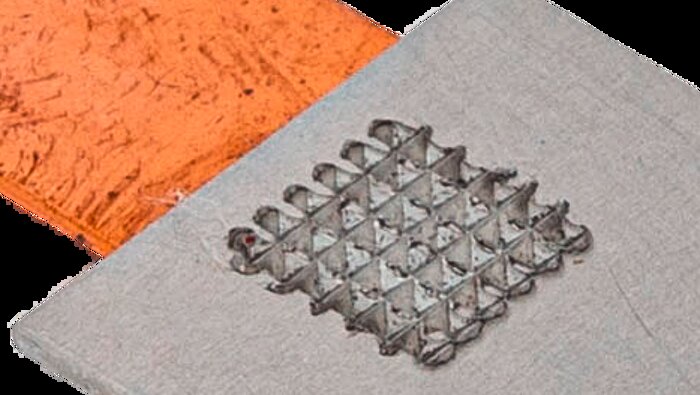
Ultrasonic welding of aluminum and copper
Welding aluminum and copper is becoming ever more important, especially due to the constantly growing market for lithium-ion batteries. These are being used more and more as for power storage, especially in the electric car industry. Aluminum and copper are primarily welded for cable and terminal connections in electronics and the automotive industry. A highly precise and reliable welding method is crucial here. Ultrasonic welding can do exactly that. Andeadvantages include the short weld time, high energy efficiency and durability of the end products.
Ultrasonic welding of copper
Just like aluminum, copper is a crucial component of many high-tech markets, including consumer electronics. The use of ultrasonic welding has proven to be highly effective in numerous applications, such as joining copper wires and other components to numerous dissimilar metals. In addition, circuit boards featuring copper elements can be assembled in a fraction of the time when using this process compared to traditional bonding techniques.
Having a process that can ensure precise and reliable welds in these sectors is critical, especially considering how small many of the elements involved can be. The efficiency of the tools used and the speed with which they work also play important roles in how important ultrasonic welding has become within these industries.
As a recognized leader in ultrasonic welding, Herrmann Ultraschall is your go-to source no matter what types of weldable metals need to be bonded for your projects. To learn more, get in touch with us today.
Benefits of ultrasonic welding of aluminum and copper:
- short welding time
- high energy efficiency
- high precision
- durability of the final products
- no consumables
Longitudinal vibrations break up the oxide layer
The energy required for joining is supplied by mechanical vibrations. The ultrasonic generator produces electrical oscillations in the 20 or 35 kHz range for this from the 50-Hz mains alternating current. A converter is used to turn the electrical oscillations into mechanical ones in the same frequency. The weld tool, called the sonotrode, transfers the vibrations to the joining partner. The sonotrode couples with the joining part facing it and makes it oscillate longitudinally. The other joining part is held in a structured anvil and does not move. The sonotrode’s coupling surface must also be structured, as otherwise the top joining partner would not move, which is to say no relative motion would be generated.
The oxide coating at the joining sites is broken up by the intensive friction and the two joining parts are fused together with a molecular bond under simultaneous exposure to pressure. The decisive aspect of the welding is not the heat produced, which is far below melting point, but the relative motion of both joining partners. As a result of the low process heat, there is no negative effect on the substance’s material structure. The joining partners’ maximum material thickness is up to 5 mm for copper sheet, depending on the weld surface. The power requirement is between 1,000 and 12,000 watts, depending on the application.
Important process visualization for ultrasonic welding of metals
The system control checks the process parameters and visualizes them. This graphical display of parameters on the machine screen, which includes amplitude, energy, weld depth and weld force, is turning out to be an important instrument to ensure process stability. A process window must be determined for each application to balance out material and production tolerances. All the upstream cell production process steps must be taken into account at this stage. It is important to reduce rejects to a minimum, especially in the case of expensive battery cells.
When determining the welding parameters, i.e. taking the application, material and production environment into account, it is essential to think holistically. Which is why it is important to get the ultrasonic technology suppliers involved in product development as early as possible. Herrmann Ultraschall sees fine parameterization as offering great opportunities to further improve the production quality and service life of sonotrodes. Correlations can be observed between process stability and particle reduction, and between energy inputs, a stable converter, and the weld tools’ service life.