Joining nonwovens using ultrasonics
Nonwovens consist of individual fibers or endless filaments (fibers of unlimited length) which form a loose cohesion. Nonwovens with thermoplastic parts (plastics which are shaped when heat is applied) can be welded using ultrasonics. Here, the plastic part of the material is heated by ultrasonics, melted and the nonwovens can be connected together (welded) without adhesive.
What is that suitable for?
Joining nonwovens without additives is perfect for hygiene products, medical engineering and cosmetics and healthcare products. Ultrasonic welding is used to:
- Laminate various layers together (e.g. for diapers)
- Incorporate embossing structures (e.g. for cotton pads)
- Separate and hemming of edge areas
- Perforate web material
How does it work?
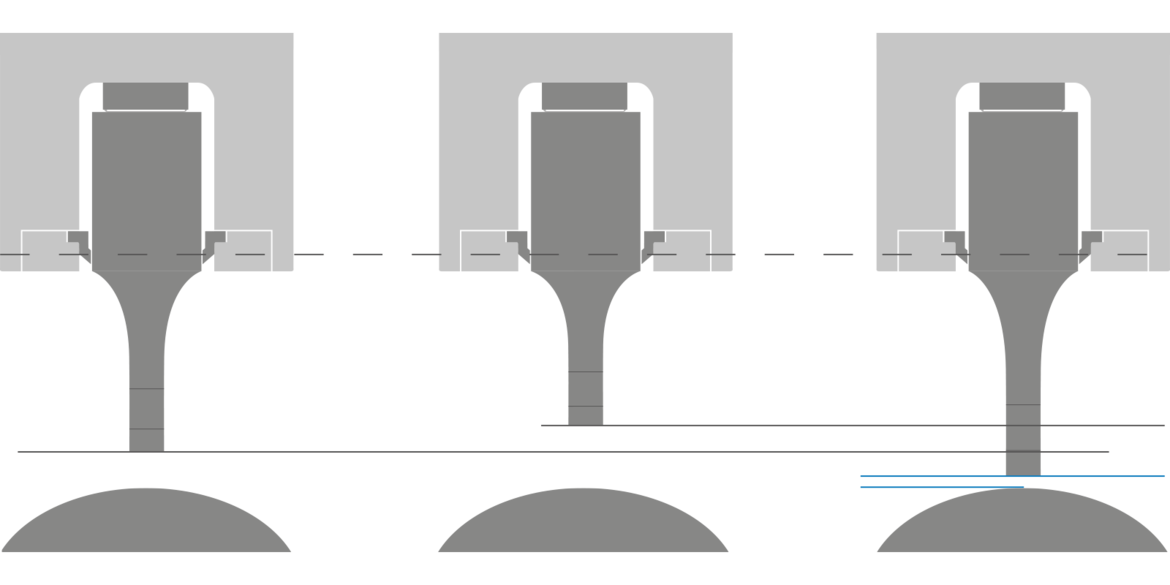
Ultrasonics are produced in the generator and transformed into mechanical vibrations in the converter. These are introduced into the material by sonotrodes. The standard frequencies here are between 20 and 35 kHz with an amplitude of 10 to 50 μm. The plastic portion of the material is stimulated, heats up and is melted. The actual weld process is fast: Thanks to the use of rotating tools such as anvil drums, up to 800 m of nonwovens can be processed per minute. The anvil drum serves as an anvil and has an individual surface structure to focus the ultrasonic energy precisely. This allows exact weld, embossing or cutting results to be achieved.
A constant distance between the material being processed and the tools is important for optimal results. This is guaranteed via the precise control technology. It ensures that the distance always remains the same, even if the weld tools change due to the heat generated during the weld process.
Welding / cross seal
Nonwovens can also be welded with a cross seal. As with the longitudinal seal, the sonotrode works in a fixed position without upward or downward movements.. The rotary anvil is what makes the difference. It ensures that the nonwovens come into contact with the sonotrode at the correct place, and are only welded there in a transverse direction. This is used for the side seams of diapers, for instance.
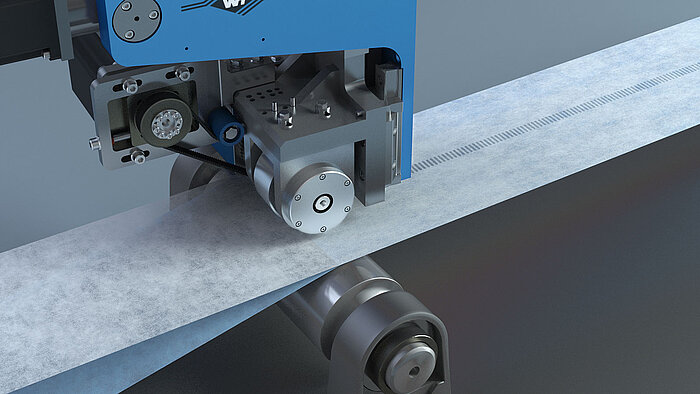
Laminating
The structure on the rotary anvil means that the nonwovens are only joined in places, unlike the longitudinal seal. This has the advantage that the material properties remain intact thanks to the many targeted connections. For example, the filter function is not affected and the material remains elastic.
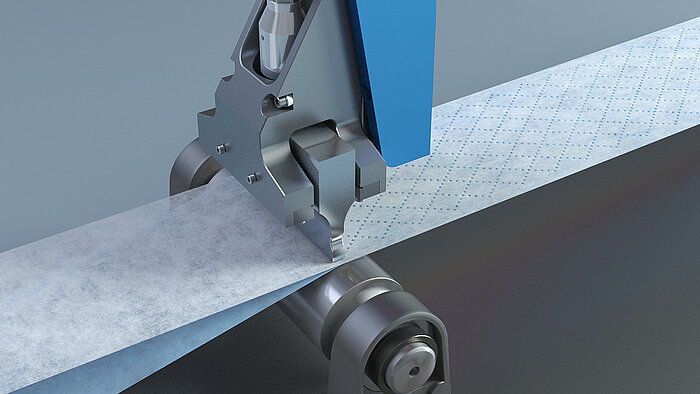
Embossing
During embossing, the nonwovens, e.g. cotton pads, have a unique structure pressed into them. This is done by an anvil drum. The special feature when the materials being joined have different colors: The color of the lower track is visible at the weld joint. A design effect, for logos, for example – without additional color printing.
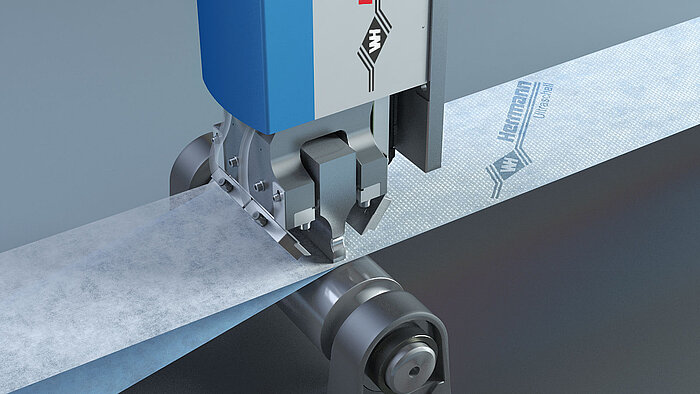
Welding nonwovens with continuous ultrasonic technology
With our ultrasonic technology we offer you processes for the continuous joining, welding, laminating, embossing, cutting of nonwovens, textiles, and thermoplastic materials. Among other things, the Hermann ultrasonics machines and systems are used for high-volume production in the textiles, medical, hygiene, filter, and general technical industries. Customers appreciate the consistently high and controlled weld quality at high speeds. This allows the realization of complex applications with user-friendly, very simple handling.