Welding plastics
In many industries, such as the automotive industry, consumer products industry or in medicine, the effective and precise joining of plastics is important. For example, the indicator lights in your car, the housing of an electric iron or a dialysis filter are all produced by joining plastics.
This can be done through a variety of different processes. Plastics can be joined using adhesive, for instance. The advantage: It isn't merely thermoplastic materials (plastics which can be shaped when heat is applied) which can be joined in this way, but also most other plastics. However, there are also disadvantages such as the long hardening process.
Thermal welding
Thermal welding is a technique in which thermoplastic materials are melted and joined using additional pressure. The condition for melting is always heat, and this is generated in different ways. In the case of hot-gas welding, for instance, warm air from the welding devices causes the melting.
Ultrasonic welding
For ultrasonic welding, sound waves with a high frequency (ultrasonic waves between 20 kHz and 70 kHz) are used. The sound waves are introduced into the plastics and cause them to heat up. Plastic welding using ultrasonics has many advantages over adhesive or conventional welding methods: It saves energy, is highly precise, requires no other tools or materials and is cost efficient. You also achieve precise and reproducible weld joints which don't require further processing.
What's the right way to weld?
Welding works by way of heat development. This is why only plastics which can be shaped when heat is applied (thermoplastic materials) can be used. In ultrasonic welding, the heat is generated by mechanical vibrations (ultrasonic waves). These stimulate the molecular chains in the plastics thereby generating friction heat. This leads to melting. When additional pressure is applied, the materials can be joined precisely.
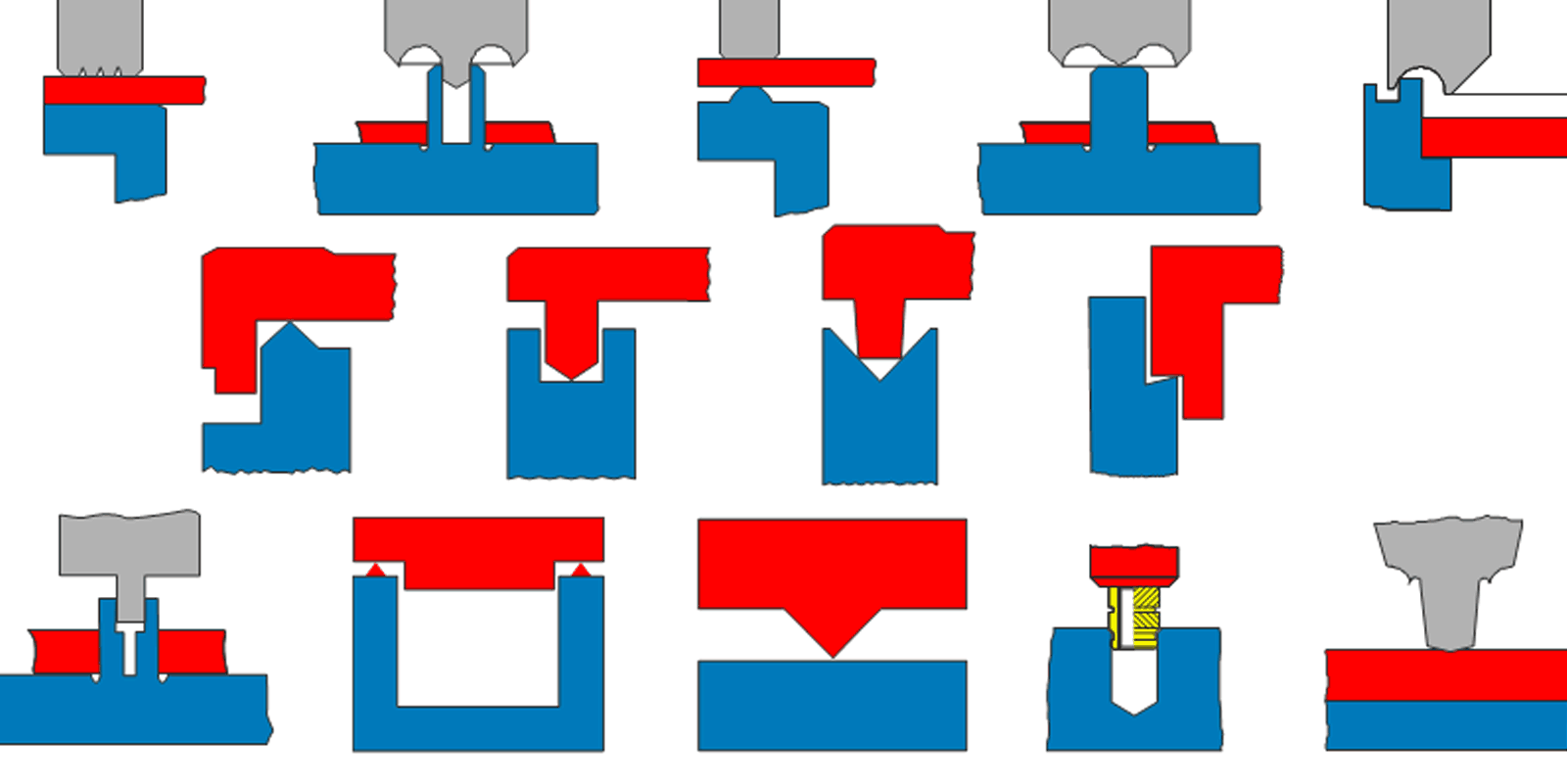
What do you need to be able to weld plastics using ultrasonics?
A generator transforms the utility frequency into a high frequency. This is transformed into mechanical vibration in the converter.The actual weld tool, the sonotrode, which is adapted individually to the application being welded, directs the oscillation into the joining area. The material heats up and melts at the points where the parts touch. The welding parts should also have a weld contour which corresponds to the material type and requirements of the joining seam.